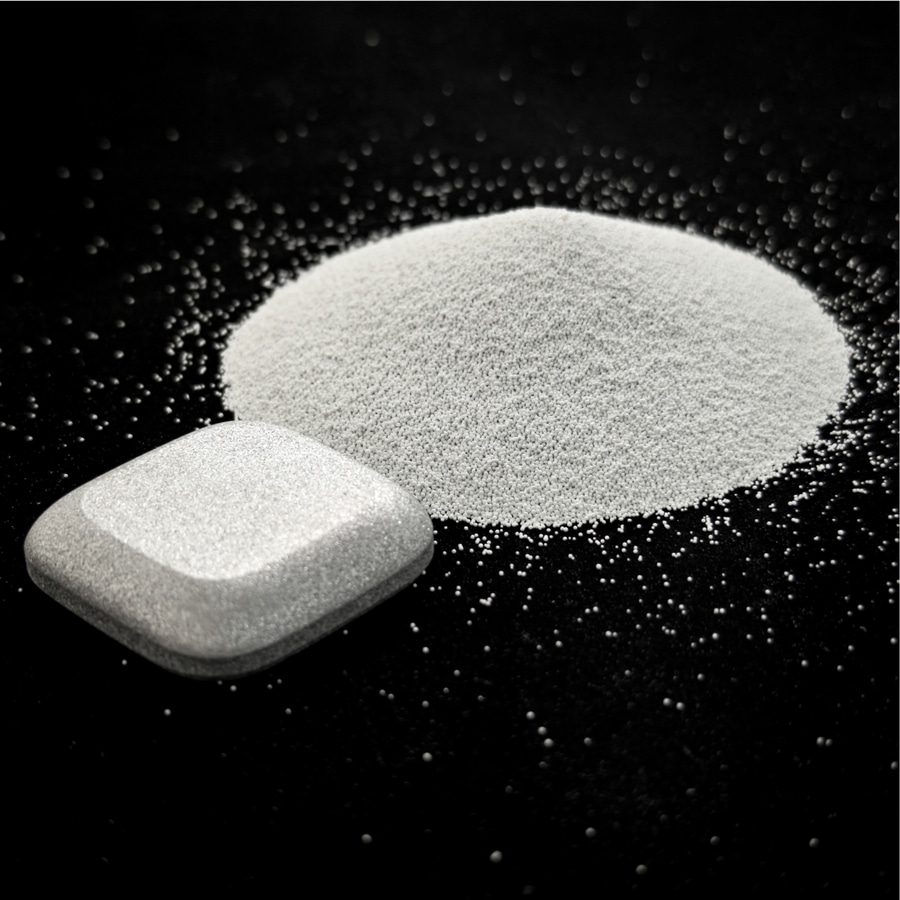
#Industry News
Optimizing Blasting Pressure and Applications for Ceramic Beads (B20–B505)
How to Match Ceramic Bead Grit Size with Blasting Pressure for Efficient and Precise Surface Treatment?
Ceramic bead blasting is widely used in industries requiring precise surface treatment, including aerospace, automotive, medical, and precision machinery. The effectiveness of this process depends on the grit size of the ceramic beads and the applied blasting pressure. From B20 to B505, different bead sizes offer varying levels of impact force, surface roughness, and material removal rates. Understanding the correlation between grit size, pressure, and application is essential for achieving optimal results.
1. Ceramic Bead Grit Sizes (B20–B505) and Their Characteristics
Ceramic beads are classified by grit size, where lower numbers (B20–B60) represent larger beads, and higher numbers (B120–B505) indicate finer particles. The size directly affects surface roughness, penetration, and material wear.
B20: 600-850µm, Aggressive cleaning and roughening
B40: 425-600µm, Heavy-duty coating removal
B60: 300-425µm, Surface preparation for adhesion
B120: 125-250µm, General-purpose cleaning and finishing
B170: 90-150µm, Satin finishing, oxidation removal
B205: 63-125µm, Delicate surface refinement
B400: 30-63µm, Fine polishing and light cleaning
B505: 10-30µm, Ultra-fine finishing, minimal material removal
Larger beads are ideal for deep cleaning and surface texturing, while finer beads create smooth, precise finishes without excessive wear.
2. Recommended Blasting Pressure for Different Grit Sizes
The effectiveness of ceramic bead blasting depends on choosing the right pressure to match the grit size. Higher pressures enhance cutting power but may lead to increased substrate wear, while lower pressures preserve material integrity.
B20-B40: 0.5–0.8 MPa (70–120 psi), Heavy-duty cleaning, rust and paint removal
B60-B120: 0.3–0.6 MPa (40–90 psi), General surface preparation, deburring
B170-B205: 0.2–0.5 MPa (30–70 psi), Oxidation removal, satin finishing
B400-B505: 0.1–0.3 MPa (15–40 psi), Ultra-fine polishing, precision surface treatment
Selecting the correct pressure prevents excessive material wear while maintaining high processing efficiency.
3. Application Scenarios Based on Grit Size
Different industries require specific grit sizes based on the desired surface treatment. Below is a breakdown of optimal applications for each range.
Coarse Grit (B20–B60) – High-Pressure (0.5–0.8 MPa)
Ideal for:
Heavy oxidation and corrosion removal on steel structures
Preparing metal surfaces for strong adhesive coatings
Cleaning industrial molds, castings, and large machinery
Medium Grit (B120–B205) – Medium-Pressure (0.3–0.6 MPa)
Ideal for:
Aerospace component surface preparation
Automotive parts finishing and deburring
Satin finishing on stainless steel and titanium alloys
Fine Grit (B400–B505) – Low-Pressure (0.1–0.3 MPa)
Ideal for:
Ultra-fine polishing of medical instruments
Surface refinement of high-precision electronic components
Delicate cleaning of glass, ceramics, and composites
4. Key Factors for Effective Blasting
To maximize performance, consider the following:
Material Compatibility: Harder metals withstand higher pressures and coarser grits, while softer materials require finer beads and lower pressures.
Nozzle Size & Shape: Larger nozzles support higher pressure and coarse beads, whereas fine beads require precision nozzles for controlled blasting.
Abrasive Reusability: Ceramic beads can be reused multiple times, but excessive recycling may reduce their effectiveness due to bead fracturing.