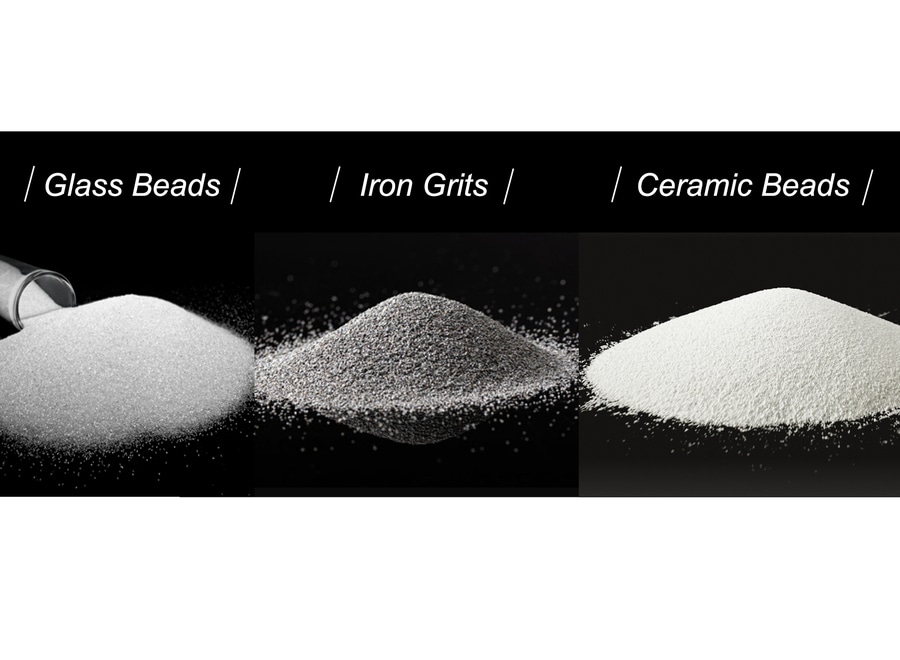
#Industry News
The Breakthrough in Surface Finishing: How Ceramic Bead Blasting is Transforming Manufacturing
Ceramic Bead Blasting Media: Redefining Durability, Precision, and Sustainability in Modern Manufacturing
1. Introduction
Blasting technology is a crucial surface treatment method in modern manufacturing, widely used for oxide removal, surface roughening, and fatigue strength enhancement. Traditional blasting media, such as quartz sand, glass beads, and aluminum oxide, suffer from significant drawbacks, including excessive dust, short lifespan, and potential damage to workpieces.
In recent years, ceramic beads (Ceramic Beads) have emerged as a high-performance alternative, gaining popularity due to their superior durability, environmental benefits, and precision surface treatment capabilities. As industries move toward smarter and greener manufacturing, ceramic bead blasting is rapidly replacing conventional media and transforming surface engineering.
2. Key Advantages of Ceramic Bead Blasting Media
2.1 Exceptional Durability and Cost Efficiency
Longer Service Life: Ceramic beads can be reused 500–1000 times, compared to 50–100 cycles for glass beads and 100–200 cycles for aluminum oxide.
Lower Consumption & Cost Reduction: With higher durability and less frequent replacement, ceramic beads reduce material waste and operational costs.
2.2 Low Dust, Health & Environmental Benefits
Minimizing Occupational Health Risks: Unlike quartz sand, which can release free silica and cause silicosis, ceramic beads eliminate such hazards.
Compliance with Green Manufacturing Standards: Producing significantly less dust, ceramic beads support cleaner production environments and help companies meet stringent environmental regulations.
2.3 Precision Surface Treatment & Enhanced Material Performance
Uniform Surface Finishing: The spherical shape of ceramic beads prevents scratches, producing consistent satin or matte finishes.
Improved Fatigue & Corrosion Resistance: The compressive stress layer formed during blasting enhances material durability, making ceramic beads ideal for aerospace and medical applications.
2.4 Lower Equipment Wear & Maintenance Costs
Minimized Equipment Damage: Unlike angular aluminum oxide or steel grit, ceramic beads’ rounded shape reduces nozzle and chamber wear, extending equipment lifespan and reducing maintenance costs.
3. Leading Applications of Ceramic Bead Blasting
3.1 Aerospace Industry
Turbine blades & engine components: Strengthening surfaces to improve fatigue resistance.
Landing gear & aircraft structures: Enhancing corrosion protection and durability.
3.2 Medical Devices
Dental implants & artificial joints: Improving surface roughness for better osseointegration and biocompatibility.
Surgical instruments: Enhancing grip and prolonging usability.
3.3 Automotive Manufacturing
Aluminum alloy wheels & engine parts: Enhancing corrosion resistance and aesthetic appeal.
Exhaust systems & brake components: Improving high-temperature performance and oxidation resistance.
3.4 Precision Molds & Tooling
Injection mold surface treatment: Improving release properties and durability.
Stamping mold blasting: Reducing wear and increasing workpiece surface quality.
3.5 Consumer Electronics & High-End Finishing
Smartphone & laptop aluminum casings: Creating premium matte textures with superior durability.
Semiconductor processing equipment: Reducing contamination for cleanroom manufacturing.
4. Future Trends in Ceramic Bead Blasting
4.1 Smart Manufacturing & Digital Monitoring
The integration of AI-powered monitoring systems will enable real-time optimization of blasting parameters, ensuring consistent quality and efficiency.
Ceramic beads’ stable performance makes them ideal for automated blasting systems in high-precision industries.
4.2 Replacing Chemical Etching for Eco-Friendly Processing
Traditional chemical etching (e.g., hydrofluoric acid for glass etching) poses environmental and safety concerns.
Ceramic bead blasting offers a clean, chemical-free “dry etching” alternative, particularly for semiconductors and display glass manufacturing.
4.3 Development of Specialized Ceramic Media for Advanced Applications
Future innovations may introduce silicon carbide (SiC) ceramic beads with higher hardness and wear resistance, suitable for deep-sea exploration and nuclear applications.
Custom-engineered ceramic media could be optimized for ultra-high-temperature resistance and corrosion-proof applications in extreme environments.
5. Conclusion
With outstanding durability, minimal dust emissions, and precision surface finishing, ceramic bead blasting is rapidly becoming the preferred choice for high-tech industries, including aerospace, medical, automotive, and electronics manufacturing.
As manufacturing transitions toward smart, sustainable, and high-precision solutions, ceramic bead blasting is poised to replace outdated media and revolutionize surface treatment technologies. The future of clean, efficient, and intelligent surface engineering belongs to ceramic bead blasting.
#CeramicBeads #BlastingTechnology #SurfaceEngineering #GreenManufacturing #PrecisionFinishing #Aerospace #MedicalDevices #SmartManufacturing