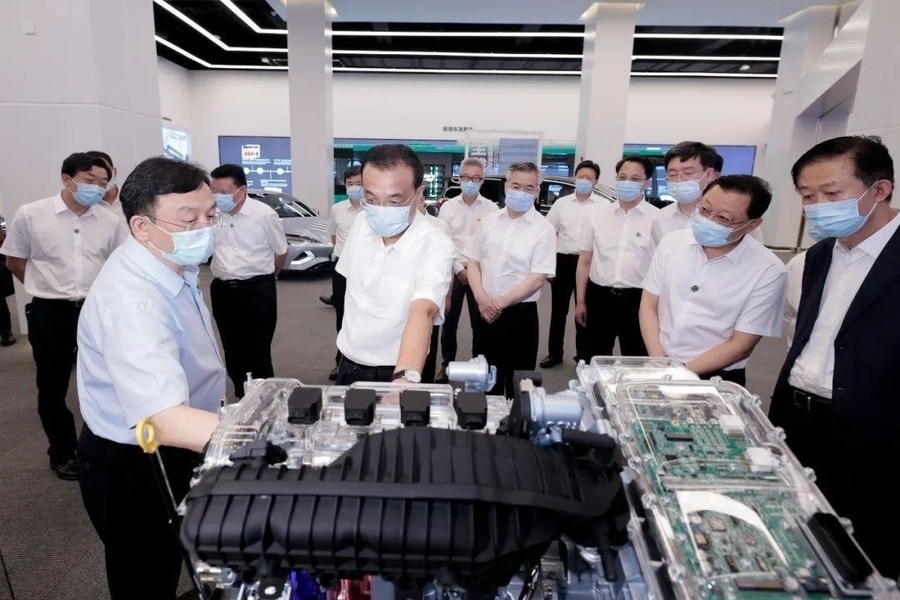
#Industry News
The Powerful Combination of Tederic and BYD
To hit the annual sales target of 2 million units, BYD and Tederic have developed strategic cooperation and introduced nearly 700 units of Tederic NEO series products.
The clamping force covers 85-1920 tons and has been installed in ten of BYD's thirteen production bases.
New energy vehicles are more cutting-edge in design, lightweight, energy-efficient, and have higher technical requirements for accessories. In addition to integrating interior and exterior trim, ambient lighting, soft and hard rubber combination, surface high-gloss parts and structural reinforcement parts, etc., all have new requirements.
At present, Tederic has achieved the development of the largest (2800 t) multi-station injection molding machine in China to replace imports, with a turntable diameter of 2800 mm. Tederic's large multi-component injection molding equipment has fully assisted BYD in replacing imports with excellent performance, serving the production of multi-color products such as headlamp masks, through-tail lamps, and various automotive interior and exterior trim parts.
Automotive optical plastic parts are thick-walled transparent plastic parts with long molding cycles. They are prone to defects such as shrinkage, shrinkage holes, dents, bubbles, and under-injection during the injection process. Secondly, the shape of the optical parts is complex. And because the special machine for optical parts must be dedicated to the machine, the energy consumption of single product production is high.
Tederic Electric's injection molding machines are also a key purchase for BYD and are used in producing optical-grade plastic parts such as through-beam guide bars, headlamp guide bars, and thick-walled lenses.

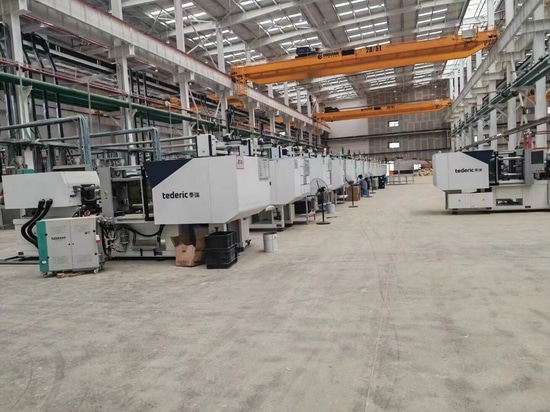
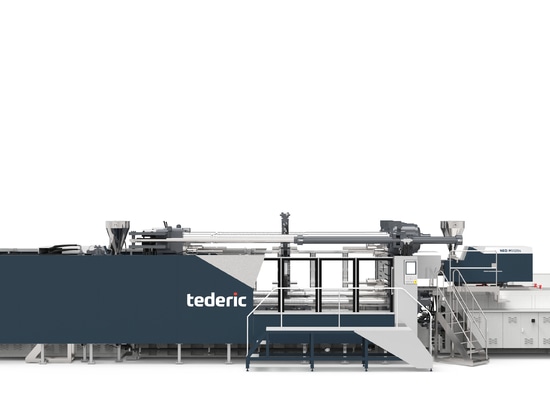
